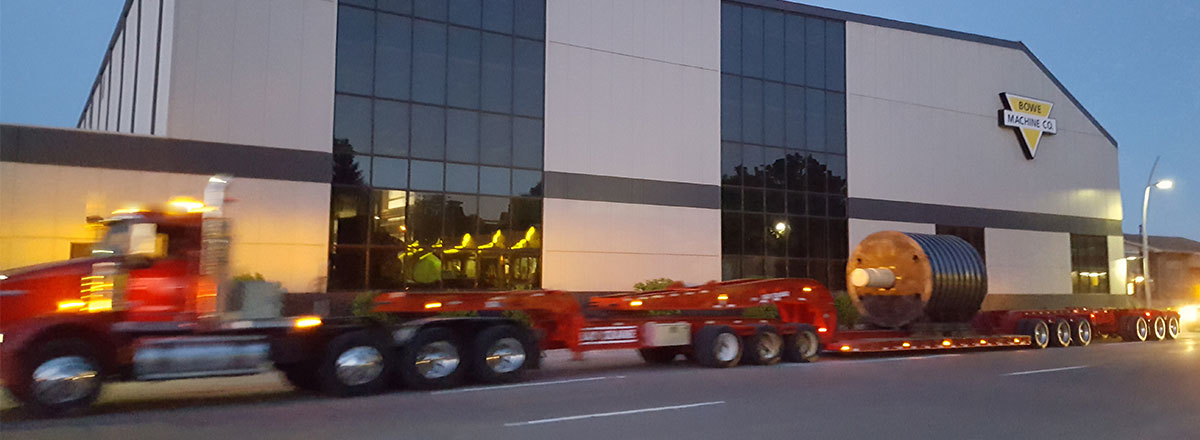
Recycling Equipment Maker Crushes Sales with IT Infrastructure Upgrade
Bowe Machine Company uses Xerox® IT Services to modernize, cut risks, and boost productivity.
“We need to be able to redirect our employees to help with sales, which helps us get more product out the door.”
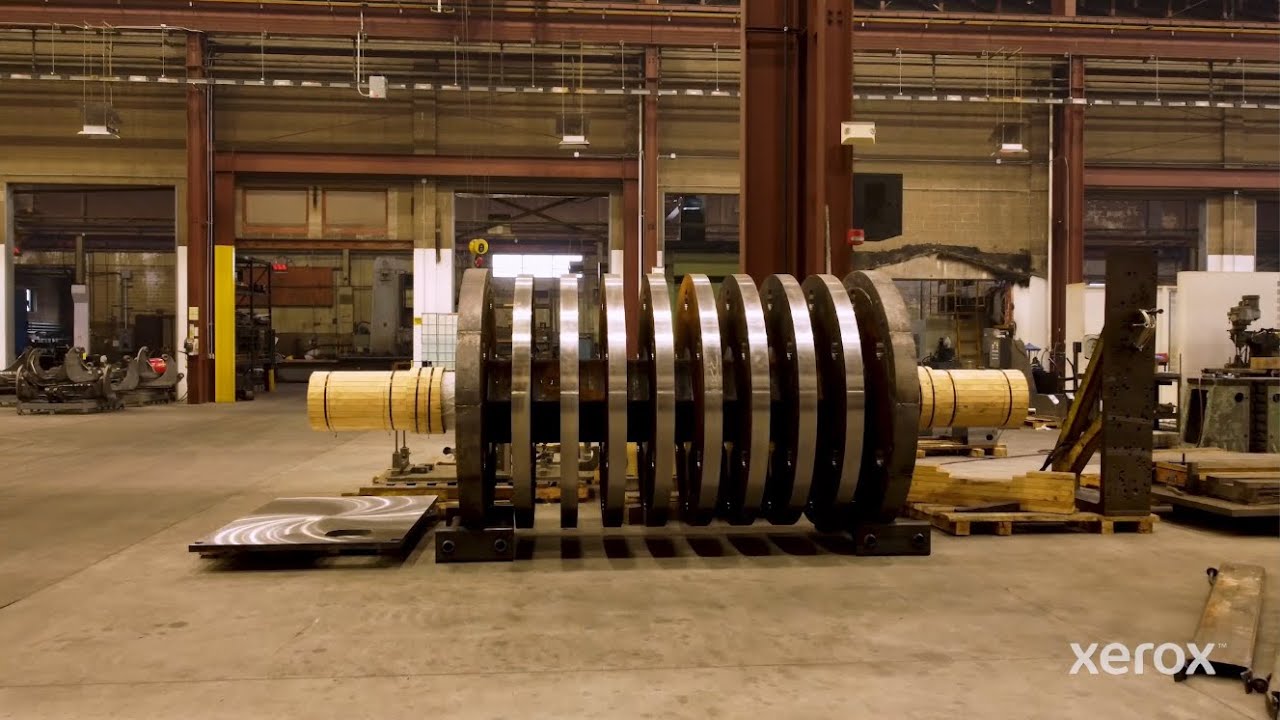
About the Client
If you’ve ever seen a video of a car being shredded for recyclable scrap, then you are familiar with the large equipment Bowe Machine Company manufactures. Founded in 1956 by Bill Bowe, the company supplies half of America’s scrapyards and makes machine parts for companies like John Deere. The Bettendorf, Iowa, company’s rotors can pick apart an automobile in 30 seconds and nearly 1,000 vehicles over the course of an eight-hour shift.
When Jeff Hassel arrived as CFO at Bowe Machine Company in 2014, he knew of Bowe’s strong manufacturing reputation, but when he conducted an IT assessment, “sirens went off right away.” Its enterprise resource planning (ERP) system ran on servers that, inexplicably, were not being backed up. “Everything we had—emails, drawings, our file system—was on these servers. You were one event from losing your information. You lose information, you can’t function,” says Hassel.
The company also had an antiquated network system and spotty Wi-Fi that was hampered by the fact that heavy-duty machinery across its sprawling plant blocked the signal. The lack of reliable internet meant running the company by spreadsheet and manual record-keeping. Cloud-based capabilities were non-existent. It was difficult for Bowe to share technical data, such as engineering assessments, both inside and outside of the company.
Bowe turned to Xerox IT Services to upgrade the company’s servers and infrastructure, creating a fast and stable Wi-Fi service and backing up crucial documents to the cloud. The company relies on Xerox Managed IT Services to provide ongoing monthly tech support. Bowe’s company files are now safely backed up to the cloud, employees are able to access and share electronic files, and team members saddled with inefficient manual processes are now able to focus on sales and customer service.
Hassell estimates that the bolstered IT infrastructure has contributed to a 10% increase in revenue.
The Challenge
Antiquated IT posed risks and inefficiencies
When Jeff Hassel became CFO of Bowe Machine Company in 2014, he faced a long line of IT hurdles. The company’s files were not being backed up, leaving it one incident away from grinding to a halt. Wi-Fi was inconsistent throughout the massive manufacturing plant because interference from heavy machinery.
Without stable internet or cloud capabilities, employees couldn’t reliably access or save electronic documents and drawings. And because the Wi-Fi was spotty, employees on the shop floor logged their hours on paper cards. Then someone had to manually enter those times.
Bowe needed an IT upgrade in order to increase efficiency and keep pace with manufacturing trends.
The Solution
Modern infrastructure and ongoing IT support
With only a single IT guy in-house, Bowe turned to RK Dixon, a Xerox™ Business Solutions company, for help. “During discovery, we pointed out outdated infrastructure and operating systems, which was a security risk,” says Don Godke, senior account executive at Xerox IT Services. “Their backups needed to be sent off-site.”
The Xerox team quickly encountered other problems. Located not far from the Mississippi River, just across from Illinois, the 80-person operation unfolds across three city blocks. The team had to find a way to ensure Wi-Fi coverage across the 99,000-square-foot plant.
The team also found that its antiquated network included switches that “didn’t have the throughput for the engineering files that they were trying to squeeze through a small fiber connection,” Godke explains.
Xerox upgraded the company’s servers and infrastructure, so the Wi-Fi became dependable and speedy—and crucial documents are now backed up in the cloud.
The team also helped Bowe deploy Xerox Managed IT Services to provide ongoing monthly tech support to maintain its infrastructure.
The Results
Secure, connected and more productive
Bowe can now fully leverage its ERP system, secure in the fact that it is properly backed up and fully connected.
“We rely heavily on our ERP system,” says Hassel. “Less running the company by spreadsheets and more network focus, which we couldn’t do before because the connectivity wasn’t great.”
Bowe’s new network has also led to greater employee productivity. With its connectivity issues resolved, Bowe has switched to electronic record-keeping, and the person once tasked with the busywork of entering staff hours can now focus on customer service.
“It went from us going from paper to all CAD (computer-aided design) -driven electronic files. [We had] lots of hurdles and those hurdles were solved by Xerox.”
In addition to building rotors, Bowe rebuilds them. When a rotor comes back into the shop, an engineering assessment is done. If there is any kind of engineering that can make that rotor stronger, that happens then. “From the standpoint of sharing engineering results inside and outside the company, upgraded tech makes that process more efficient,” says Hassel. “If you have the IT infrastructure, you’re better able to utilize the software [like data sharing] that sits on there. If you don’t, then it’s hard to use that as a tool.”
By providing tech support every month, Xerox has alleviated some burden off Bowe’s sole IT employee, who can now spend more time with employees for performance and satisfaction.
And, even though as an essential company Bowe never had to close for the pandemic, the company’s now-reliable network allows employees to work from home if necessary.
With the help of Xerox, this family-owned business, which grew from a rented one-room shop to take over three city blocks, can keep on, well, crushing it.
The Challenge
Lack of backup system for ERP put company operations at risk
Spotty Wi-Fi and antiquated network system
Single IT employee meant inadequate tech maintenance
Unable to share/access electronic documents
Employee inefficiencies due to manual tasks
The Solution
Xerox IT Services evaluated and upgraded IT infrastructure
Xerox Managed IT Services to provide ongoing monthly tech support
The Results
New infrastructure provides secure backup of company information
Speedy and reliable Wi-Fi and a network that can handle transmission of large files
Employees are able to access and share electronic files
Increased employee productivity due to elimination of manual tasks
An estimated 10% increase in revenue
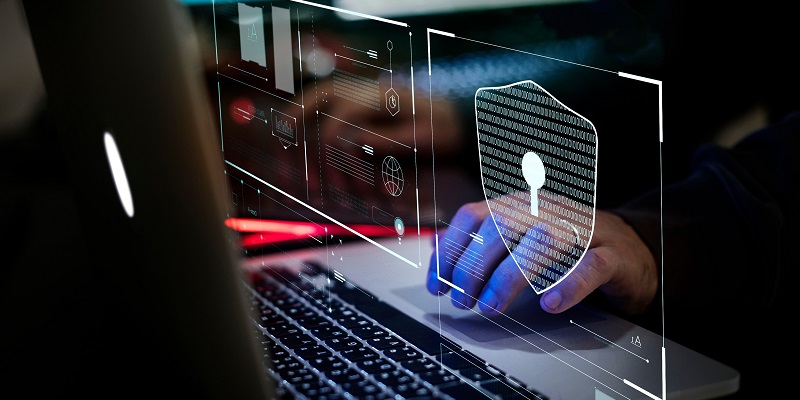
End-to-end IT Services and Solutions
We offer 24/7/365 IT support services for your small business or medium business with a personalized suite of IT solutions.
Is work getting in the way of work?
From automated filing systems to managed IT services, and everything in between.
Follow us on LinkedIn to stay up to date on all the latest from Xerox — including news, innovation, and big announcements.
Related Articles
Xerox and ITsavvy Join Forces to Address Your IT Challenges
Xerox and ITsavvy's IT solutions are bringing IT services to more areas across the US, Canada, and U.K. with Generative AI, cybersecurity protection, and digital transformation solutions.
Essential Cybersecurity Insurance Protection for SMBs
Learn how Xerox ensures small and medium-sized businesses qualify for cyber insurance and are protected against cybersecurity threats.
Transforming Triumph Business Capital
Discover how Triumph Business Capital leveraged Xerox IT Solutions to streamline their operations and achieve business success.
Xerox IT Solutions Keeps Transportation Company Up and Running
See how Xerox IT Solutions reduced business downtime by optimizing It Infrastructures for a major transportation company in this case study.
PharmaJet Brings Needle-Free Vaccine Injections to the World, with an Assist from Xerox
The Denver-based company partnered with Xerox to overhaul its IT systems, allowing them to seamlessly transition to Work From Anywhere at just the right time.
Xerox speeds up car dealership
Mountains of paper slowed Ron Bouchard Auto Stores until Xerox redesigned the company’s workflows so it can devote more time to its customers.